Ваз головка 2101
ДОРАБОТКА ГОЛОВКИ БЛОКА ЦИЛИНДРОВ ВАЗ-2101
Для начала расчеты. Тупо площади считаем.
Впускной канал, самая узкая часть - там, где выпирает направляющая. (29*29*3,1415/4)-(14*14*3,1415/4) = 660 - 154 = 506 мм2
Щель впускного клапана в максимальном подъеме: 33*3,1415*10 = 1037 мм2
Отсюда видно, что размеры канала значительно уступают по сравнению с другими узкими местами впускного тракта. Это действительно только в момент полного открытия клапана, но это время почти полного открытия подавляющее. Короче, нада делать. Максимум (покажу на фото) - это 34мм, на большее стандартный коллектор не расточить, стенка 1мм остается.
Считаем с учетом того, что клапанную ножку обточим до 7мм, а направляющую срежем заподлицо: (34*34*3,1415/4)-(7*7*3,1415/4) = 909 - 39 = 870 мм2 получается, увеличиваем площадь самого узкого места на 70%, неплохо...
От составителя: Двигатель 1300, ГБЦ 2101, система питания – Webber 2101 23х24
Далее голова снимается с машины, разбирается и моется. Шикарно конечно моется углекислотой, но не было огнетушителя под рукой. Мыл обычным керосином, а потом в ванной щеткой с порошком.
Кстати, нужно не забыть смазать маслом все стальные детали (направляющие, седла, втулки под рокера), чтоб ржа не схватила. Еще неплохой по слухам метод, когда ВД40 растворяется в незамерзайке. жидкости для омывателя - получается белая эмульсия, которая все смывает легко...Шпильки, кстати, лучше тоже скрутить, но мне покуда не мешали...
Пациент:
Направляющие выбиваются приспособлением, которое я изготовил из болта. Выбиваются легко и непринужденно... наружа приспособы 13.5, внутренний штырь для направления - 8мм.
Теперь все готово для пиления каналов. Я бы советовал начинать с коллектора, поскольку в голове запаса металла по краям больше, лучше подгонять голову под коллектор а не наоборот...
Замеры: каналы в голове 29, выпуск 27, в коллекторе - 29, вып. коллектор 29.
растачивал я шкуркой в дрели. Самая эффективная головка ИМХО - это вал (в моем случае сверло толстое), на который наматывается ветошь, а на нее - полоса шкурки дето в 20см длиной (ессно все внахлест мотается, чтоб не соскакивало)
Использовал я самую грубую шкурку НА ТРЯПИЧНОЙ ОСНОВЕ какая только была под рукой - это 24-ка. Один канал в голове я ею делал за 2 часа. Также для удобства сделал наборчик шайб на палочке (см. фото), номинальной (34мм) и уменьшенного диаметра (33) и комплект для выпуска. Такими ну очень удобно контролировать диаметр канала, чтоб не махнуть лишку - такая шайба должна свободно проходить по каналу перпендикулярно оси, и не сильно болтаться.
Технология - мотаем ветошь со шкуркой так, чтобы "головка" еле лезла в дырку, начинаем сверлить потихоньку пропихивая все дальше, покуда шкурка не рассыплется. Потом можно кусок оторвать или перевернуть полоску и заново... Контролируем диаметр шайбой, новую полосу шкурки и заново поехали... неплохо бы еще заиметь инструмент для измерения толщины стенок, но я пользовался пинцетом с налепленными на концы кусочками пластилина.
Коллектор: разительно отличаются по диаметру пропиленные каналы от не пропиленных:
коллектор точится значительно тяжелее чем голова, из-за того, что можно подлезть только с одной стороны (со стороны карба не сильно то и просунешься).
Смог пропилить коллектор до 34-х только на 2/3, пришлось устранить сверлом перегородку между каналами: как было
как стало
Все, шайбы свободно проходят:
Теперь очередь головы.
нужно состыковать каналы коллектора с головой. Пробовал разные варианты с отпечатками и проч... сложно все это как-то... Остановился на пластелине - леплю по окружности на голове, смачиваю водой коллектор, прижимаю рукой, отпускаю, выдавленный пластилин внутрь коллектора срезаю - четко видно, куда нада править голову. Поправить лучше отдельно перед расточкой, потому что шкурка раздает во все стороны одинаково. Поправить можно напильником круглым, я просто грубо обтесал дырку в нужную сторону, чтобы она равномерно повторяла контур дыры в коллекторе. Кстати, лучше выход из головы сделать чуть побольше, например 35, потому что ступенька все равно будет, лучше чтобы она была не в сторону головы. Но специально расширять не нада - 35 и так получится от постоянного шныряние шкуркой через эту дырку.
А потом поехали... Растачиваем равномерно со стороны коллектора, покуда шайба не будет пролазить до дырки под направляющую, потом лучше точить со стороны КС. С этой стороны осторожнее с седлами!!! Растачиваются они на удивления быстро и легко, можно полностью уничтожить место под фаску. разница очевидна:
Хорошо видно, как убирается нарост вокруг дырки под направляющую, который очень неслабо закрывает канал:
Каналы все пропилены, голова вымыта. Не забыть все стальные части перед мойкой смазать маслом, седла клапанов в первую очередь!). Для промывки системы охлаждения использовал электролит для акку - т.е. серную кислоту. Перевернул голову вверх тормашками, закупорил все отверстия и аккуратно, чтоб кислота не попала на наружную поверхность головы (она все ж алюминий хорошо ест), заливал внутрь, медленно покачивая голову. Накипь, налет и ржа растворяется полностью за несколько секунд, полный цикл возни головы в кислоте не думаю, что нужно растягивать более чем на 5 минут. Также аккуратно кислоту сливаем. На фото отлично виден уровень стояние кислоты - сверху все грязно, снизу девственно чистый алюминий:
После голову сразу промыть, можно в растворе соды или стирального порошка и побыстрее высушить. Например, в духовке =)
Итого:
впуск коллектор 34 (было 29), каналы 34 (было 29), седла 33.5 (было 32.5) выпуск каналы у седла 28 (было 27, наполовину перекрыты выступом под направляющую), на выходе из головы 30 (было 27), коллектор 30(таким и был), седла 28 (были 27.5).
Ушло 0.5 м2 шкурки №24 и гдето столько же ветоши. На канал в впускном коллекторе уходило 2 часа, в голове впуск - 1 час. В голове выпуск - пол часика...
Нарезал небольшие ушки в КС:
Результаты - в голове глядя на вход в канале, можно увидеть выход, в недоработанной такого нет:
Теперь насчет направляющих. Тщательно взвесив все за и против, решил остановиться на своем варианте и пилить ее сложно-пространственно
Для начала разметил на ней метчиком линию, по которой она торчит в канале, также по всему периметру (чтоб легко точить и потом запрессовывать) прочертил ее перед и зад.
Смысл был в том, чтобы максимально снять торчащего металла, и в то же время оставить по максимуму по площади канал изнутри (масло) и не трогать вообще ее нагруженную сторону (разобъет), и при этом все максимально аэродинамично сгладить. Впускные получились по оконцовке такими:
Как видно, на пятке (та сторона, на которую давит при работе клапан) я практически не трогал металл, поэтому вряд-ли деформируется.
С выпускными немного тяжелее - там и отвод тепла и нагруженность сильнее, и направление потока больше. Поэтому смысл такой-же, но объем работ значительно меньше:
Вот так торчит стандартная (тока покоцанная немного) в обработанном впускном канале:
вот так - обработанная (правда не до конца выведена, это бушная, я ее точил на пробу)
Доработал клапана... Тяжеловато было, резец очень плохо берет, даже победитовый... Новый выпускной клапан практически вообще не берется, мне советовали на доработку брать только б/у, они лучше точатся - материал мягче. Зато потом зажал в дрель и доводил форму шкуркой - берется на ура! Медленно зато уверенно снимается металл. Вот что получилось в итоге:
Снимался металл вот так:
(обработанная фотка стокового впускного клапана, красным - снятый металл)
Запрессовал направляющие изготовленной оправкой (стальной прут, внутри отв. 11.0мм) Голова в духовке до 100 град, направляющие в морозилку. Забивать надо аккуратно, но очень быстро. Не забыть снять шпильки распреда, они будут мешаться (без снятия крайних вообще не запрессовать). Сначала лезет легко потом нагреваются, но все равно лезут нормально. Выбивались, чесслово, с гораздо большим усилием. Главное, шустрее орудовать.
Фото впуска с клапаном:
Выпуск с клапаном
ГТЖ вместо 135/125 ввинтил 140/140. Немного покатался для небольшой приработки, померился.
Как и следовало ожидать, ровный рост КМ по всей кривой, увеличение оборотов ММ, увеличение КП. Прибавка получилась 14 лошадей (ну или 12, если учесть, что в молодости мотор имел 75), на что предварительно и рассчитывалось.
Ну, думаю, окончательной тарировкой карба еще одну-другую лошадку сниму (поскольку вроде и так едет нормально, без провалов)
Если все мои изыскания сжать в единый временной промежуток и выбросить эстетику (вроде надраивания до блеска головы), то в 5 рабочих дней уложиться можно легко. 1 день - снятие-установка-настройка, 3 дня пиления и 1 день на расслабоне посвятить можно клапанам.
Источник: www.vaz.ee Автор: Андреем Кушпелем (Oxygen)
gbc-servise.narod.ru
ТЮНИНГ КАК СТИЛЬ ЖИЗНИ » Статьи » ВАЗ » Двиг. и трансмиссия » Доработка ГБЦ 2101(1)
Для начала расчеты. Тупо площади считаем.
Впускной канал, самая узкая часть - там, где выпирает направляющая. (29*29*3,1415/4)-(14*14*3,1415/4) = 660 - 154 = 506 мм2
Щель впускного клапана в максимальном подъеме: 33*3,1415*10 = 1037 мм2
Отсюда видно, что размеры канала значительно уступают по сравнению с другими узкими местами впускного тракта. Это действительно только в момент полного открытия клапана, но это время почти полного открытия подавляющее. Короче, нада делать. Максимум (покажу на фото) - это 34мм, на большее стандартный коллектор не расточить, стенка 1мм остается.
Считаем с учетом того, что клапанную ножку обточим до 7мм, а направляющую срежем заподлицо: (34*34*3,1415/4)-(7*7*3,1415/4) = 909 - 39 = 870 мм2 получается, увеличиваем площадь самого узкого места на 70%, неплохо...
Абсолютные данные не точные, но в сравнении - ценная информация.
От составителя: Двигатель 1300, ГБЦ 2101, система питания Webber 2101 23х24
Далее голова снимается с машины, разбирается и моется. Шикарно конечно моется углекислотой, но не было огнетушителя под рукой. Мыл обычным керосином, а потом в ванной щеткой с порошком. Кстати, нужно не забыть смазать маслом все стальные детали (направляющие, седла, втулки под рокера), чтоб ржа не схватила. Еще неплохой по слухам метод, когда ВД40 растворяется в незамерзайке. жидкости для омывателя - получается белая эмульсия, которая все смывает легко...
Шпильки, кстати, лучше тоже скрутить, но мне покуда не мешали...
Пациент:
Направляющие выбиваются приспособлением, которое я изготовил из болта. Выбиваются легко и непринужденно... наружа приспособы 13.5, внутренний штырь для направления - 8мм.
Теперь все готово для пиления каналов. Я бы советовал начинать с коллектора, поскольку в голове запаса металла по краям больше, лучше подгонять голову под коллектор а не наоборот...
Замеры: каналы в голове 29, выпуск 27, в коллекторе - 29, вып. коллектор 29.
растачивал я шкуркой в дрели. Самая эффективная головка ИМХО - это вал (в моем случае сверло толстое), на который наматывается ветошь, а на нее - полоса шкурки дето в 20см длиной (ессно все внахлест мотается, чтоб не соскакивало)
Использовал я самую грубую шкурку НА ТРЯПИЧНОЙ ОСНОВЕ какая только была под рукой - это 24-ка. Один канал в голове я ею делал за 2 часа. Также для удобства сделал наборчик шайб на палочке (см. фото), номинальной (34мм) и уменьшенного диаметра (33) и комплект для выпуска. Такими ну очень удобно контролировать диаметр канала, чтоб не махнуть лишку - такая шайба должна свободно проходить по каналу перпендикулярно оси, и не сильно болтаться.
Технология - мотаем ветошь со шкуркой так, чтобы "головка" еле лезла в дырку, начинаем сверлить потихоньку пропихивая все дальше, покуда шкурка не рассыплется. Потом можно кусок оторвать или перевернуть полоску и заново... Контролируем диаметр шайбой, новую полосу шкурки и заново поехали... неплохо бы еще заиметь инструмент для измерения толщины стенок, но я пользовался пинцетом с налепленными на концы кусочками пластилина.
Коллектор: разительно отличаются по диаметру пропиленные каналы от не пропиленных:
коллектор точится значительно тяжелее чем голова, из-за того, что можно подлезть только с одной стороны (со стороны карба не сильно то и просунешься).
Смог пропилить коллектор до 34-х только на 2/3, пришлось устранить сверлом перегородку между каналами: как было
как стало
Все, шайбы свободно проходят:
Теперь очередь головы.
нужно состыковать каналы коллектора с головой. Пробовал разные варианты с отпечатками и проч... сложно все это как-то... Остановился на пластелине - леплю по окружности на голове, смачиваю водой коллектор, прижимаю рукой, отпускаю, выдавленный пластилин внутрь коллектора срезаю - четко видно, куда нада править голову. Поправить лучше отдельно перед расточкой, потому что шкурка раздает во все стороны одинаково. Поправить можно напильником круглым, я просто грубо обтесал дырку в нужную сторону, чтобы она равномерно повторяла контур дыры в коллекторе. Кстати, лучше выход из головы сделать чуть побольше, например 35, потому что ступенька все равно будет, лучше чтобы она была не в сторону головы. Но специально расширять не нада - 35 и так получится от постоянного шныряние шкуркой через эту дырку.
А потом поехали... Растачиваем равномерно со стороны коллектора, покуда шайба не будет пролазить до дырки под направляющую, потом лучше точить со стороны КС. С этой стороны осторожнее с седлами!!! Растачиваются они на удивления быстро и легко, можно полностью уничтожить место под фаску. разница очевидна:
Хорошо видно, как убирается нарост вокруг дырки под направляющую, который очень неслабо закрывает канал:
Каналы все пропилены, голова вымыта. Не забыть все стальные части перед мойкой смазать маслом, седла клапанов в первую очередь!). Для промывки системы охлаждения использовал электролит для акку - т.е. серную кислоту. Перевернул голову вверх тормашками, закупорил все отверстия и аккуратно, чтоб кислота не попала на наружную поверхность головы (она все ж алюминий хорошо ест), заливал внутрь, медленно покачивая голову. Накипь, налет и ржа растворяется полностью за несколько секунд, полный цикл возни головы в кислоте не думаю, что нужно растягивать более чем на 5 минут. Также аккуратно кислоту сливаем. На фото отлично виден уровень стояние кислоты - сверху все грязно, снизу девственно чистый алюминий:
После голову сразу промыть, можно в растворе соды или стирального порошка и побыстрее высушить. Например, в духовке =)
Итого:
впуск коллектор 34 (было 29), каналы 34 (было 29), седла 33.5 (было 32.5) выпуск каналы у седла 28 (было 27, наполовину перекрыты выступом под направляющую), на выходе из головы 30 (было 27), коллектор 30(таким и был), седла 28 (были 27.5).
Ушло 0.5 м2 шкурки №24 и гдето столько же ветоши. На канал в впускном коллекторе уходило 2 часа, в голове впуск - 1 час. В голове выпуск - пол часика...
Нарезал небольшие ушки в КС:
Результаты - в голове глядя на вход в канале, можно увидеть выход, в недоработанной такого нет:
Теперь насчет направляющих. Тщательно взвесив все за и против, решил остановиться на своем варианте и пилить ее сложно-пространственно
Для начала разметил на ней метчиком линию, по которой она торчит в канале, также по всему периметру (чтоб легко точить и потом запрессовывать) прочертил ее перед и зад.
Смысл был в том, чтобы максимально снять торчащего металла, и в то же время оставить по максимуму по площади канал изнутри (масло) и не трогать вообще ее нагруженную сторону (разобъет), и при этом все максимально аэродинамично сгладить. Впускные получились по оконцовке такими:
Как видно, на пятке (та сторона, на которую давит при работе клапан) я практически не трогал металл, поэтому вряд-ли деформируется.
С выпускными немного тяжелее - там и отвод тепла и нагруженность сильнее, и направление потока больше. Поэтому смысл такой-же, но объем работ значительно меньше:
Вот так торчит стандартная (тока покоцанная немного) в обработанном впускном канале:
вот так - обработанная (правда не до конца выведена, это бушная, я ее точил на пробу)
Доработал клапана... Тяжеловато было, резец очень плохо берет, даже победитовый... Новый выпускной клапан практически вообще не берется, мне советовали на доработку брать только б/у, они лучше точатся - материал мягче. Зато потом зажал в дрель и доводил форму шкуркой - берется на ура! Медленно зато уверенно снимается металл. Вот что получилось в итоге:
Снимался металл вот так:
(обработанная фотка стокового впускного клапана, красным - снятый металл)
Запрессовал направляющие изготовленной оправкой (стальной прут, внутри отв. 11.0мм) Голова в духовке до 100 град, направляющие в морозилку. Забивать надо аккуратно, но очень быстро. Не забыть снять шпильки распреда, они будут мешаться (без снятия крайних вообще не запрессовать). Сначала лезет легко потом нагреваются, но все равно лезут нормально. Выбивались, чесслово, с гораздо большим усилием. Главное, шустрее орудовать.
Фото впуска с клапаном:
Выпуск с клапаном
ГТЖ вместо 135/125 ввинтил 140/140. Немного покатался для небольшой приработки, померился.
Как и следовало ожидать, ровный рост КМ по всей кривой, увеличение оборотов ММ, увеличение КП. Прибавка получилась 14 лошадей (ну или 12, если учесть, что в молодости мотор имел 75), на что предварительно и рассчитывалось.
Ну, думаю, окончательной тарировкой карба еще одну-другую лошадку сниму (поскольку вроде и так едет нормально, без провалов)
Если все мои изыскания сжать в единый временной промежуток и выбросить эстетику (вроде надраивания до блеска головы), то в 5 рабочих дней уложиться можно легко. 1 день - снятие-установка-настройка, 3 дня пиления и 1 день на расслабоне посвятить можно клапанам.
Идеи, расчеты и работа произведена: Андреем Кушпелем (Oxygen) Составил и отредактировал: Pugnator
www.vaz.ee
ГБЦ ВАЗ 2106, 2101, 2102, 2107, 2105 классика
Содержание статьи:
-
Доработка ГБЦ ВАЗ 2101
-
Расточка ГБЦ ВАЗ 2105
-
ГБЦ прирезка седел и притирка клапанов ВАЗ 2101
-
Капремонт ГБЦ ВАЗ 2106
-
Замена прокладки ГБЦ ВАЗ 2107
- Замена направляющих ВАЗ 2101
1. Доработка ГБЦ ВАЗ 2101
Рассказ в основном будет про то, как дорабатывал ГБЦ:
расточенная ГБЦ 33х29
После разборки блока пришло время разбирать ГБЦ. Для этого мне был необходим инструмент: рассухариватель и выбивалка для направляющих клапанов. Это всё было куплено. Выбивалка универсальная, для ремонта двигателя.
Сохранить в Альбомоправка универсальная
Цены:
1. Рассухариватель — 120 рублей 2. Набор оправок — 200 рублей 3. Ключ для притирки клапанов – 70 рублей
Итак, разобрал ГБЦ:
ГБЦ разобрана
Все разбирал без книжки, скажем так по интуиции. Люблю очень всё додумывать сам, как и что разбирается и делается. к тому же при полном понимании работы системы. Из особенностей при разборке скажу одно: некоторые клапана не хотят рассухариваться. Это не повод расстраиваться. Берёте свечной ключ, ставите на тарелку клапана и бьёте молотком или кувалдой. Затем, снова берёте рассухариватель и всё идеально рассухаривается. При знании этого метода вы рассухарите клапаны за 5 минут. Направляющие выбиваются просто, с этим труностей не будет никаких. Правило такое: выбивать на холодной ГБЦ, забивать на горячей. Тогда всё будет как надо.
Разложил все запчасти по полочкам аккуратно, чтобы под ногами не валялось и всё было правильно и чётко. надо было так с самого начала разбора движки делать…всё приходит с опытом.
Затем пришло время распила впускного коллектора и ГБЦ. После тренировки расточки каналов на пробном коллекторе понял свою ошибку – увожу канал не туда. Это не очень хорошо. Думаю, что не у меня одного эта ошибка была. Вот в чём она заключается:
криво расточенный коллектор
Слева ровный неуведенный канал, справа кривой и уведённый) разница я думаю заметна всем. Каков же способ ровной расточки канала? Нашел как избежать такого увода канала, чтобы всё было ровно и каналы были круглые. Этот способ просто банальное рисование. Каналы коллектора по своей природе ровные и круглые (в отличии от каналов ГБЦ). Поэтому отмеряете сколько вам нужно с каждой стороны миллиметров и рисуете - вот так:
как не увести каналы и быть умничкой
И канал вы теперь точно не уведете. Будете знать в каком направлении двигаться. Очень удобный метод. Всем советую. Семь раз отмерь, один раз отрежь. Точу каналы наждачкой, да это муторно, согласен, но всё же надежно. Впилиться в канал охлаждения шансы малы. Поэтому работается намного спокойнее. Инструмент, как и все используют: дрель -> шланг, надетый чуть-чуть и затянутый хомутом -> ткань (ветошь) -> шкурка намотанная внахлёст. Минус этого инструмента — часто рвутся шланги. После долгого пиления каналов, отмывания и наружного шкурения коллектора вышло вот так:
расточенный коллектор
Ура. Коллектор расточен. Каналы 32-33 мм в диаметре. То есть выпускной клапан проваливается и болтается в канале. Точить коллектор очень муторно. Проблема заключается в постоянно рвущихся шлангах…поэтому запаситесь терпением. После того как коллектор расточил, решил поехать закупиться некоторыми ништяками:
все для ГБЦ и не только
по блоку
Итак, вот полный список и цены на все детали: 1. Развёртка для направляющей клапана – 200 рублей 2. Шпильковёрт — 100 рублей 3. Сцепление VALEO – 2700 рублей 4. Вкладыши коренные и шатунные ЗМЗ – 185 и 149 рублей 5. Комплект прокладок двигателя – 495 рублей 6. Кольца SM – 715 рублей 7. Масляный фильтр SCT – 121 рубль 8. Успокоитель — -54 рубля 9. Башмак натяжителя – 45 рублей 10. Пальцы – 160 рублей. Но взял не те. Мне нужны от 2108… 11. Клапана AMP (Польша) – 900 рублей 12. Направляющие АвтоВАЗ 2101 – 270 рублей 13. Рокера АвтоВАЗ – 850 рублей 14. Постель распределительный валвала АвтоВАЗ – 400 рублей 15. Оправка для колец – 250 рублей 16. Зенковки – 900 рублей 17. Кольца стопорные, болт кпп, гайка храповика – 200 рублей Вроде, ничего не упустил.
Теперь пришло время распила ГБЦ.
1. Всё начинается с совмещения каналов с коллектором. Для этого нам понадобится металлическая трубка. Лично я купил в сантехническом магазине медный соединитель двух проводков походу, Он идеально подошел для моего дела. Берём его. Стачиваем до нужного радиуса чтобы потом вставить в каналы охлаждения коллектор — ГБЦ, тем самым получив недвижимое их соединение друг с другом, так сказать без люфта. Совмещение очень важно в распиле ГБЦ, этим нельзя пренебрегать. Иначе вся ваша работа будет выполнена насмарку при неправильном совмещении…итак, получили вот такую деталь
будущий штифт
2. После подгона, обрезания и тд получаются вот такие штифты в каналах охлаждения. Важно сделать так чтобы он стояли плотно, не выпадали и не шатались.
штифты
3. С подгоном закончил. Коллектор ровно и не шатаясь стоит на ГБЦ. Цель достигнута. Теперь берем обычный пластилин и обклеиваем им канал вот таким образом
зеленый пластилин на канале
4. Затем посыпаем его любой металлической крошкой (нужно для того чтобы пластилин не прилипал к коллектору который будет в дальнейшем прислоняться)
зеленый пластилин обсыпанный золотой крошкой
5. Прислоняем коллектор и на пластилине видим отпечатки каналов:
отпечатки каналов коллектора видны на пластилине
6. Отрезаем продавленный пластилин канцелярским ножиком, тем самым делая царапины и просто убирая лишнее, кладём новый пластилин между тем, который был положен ранее…и повторяем всё те же операции
7. В конце концов вырисовывается вот такое очертание, как надо пилить канал, чтобы всё ровненько совместилось. Скажете криво вырисовалось? Ан нет. Сам сначала подумал, что я накосячил. Потом после прочтения в интернете кучи тем по этому вопросу, увидел, что так совмещается абсолютно у всех.
как надо пилить
После проверки клапаном, оказалось, получилось всё просто идеально. Клапан скользит по каналам ничего не задевая, как будто это один единый канал. Совмещением я очень и очень доволен. Не ожидал такого блестящего результата. Вот, пожалуй, всё, что я хотел рассказать про совмещение, а то многие вопросы задают, буду надеяться, что такое объяснение пригодится. Что скажу по самому распилу каналов ГБЦ? 1. Пилятся намного быстрее и лучше, чем каналы коллектора. Из-за отсутствия гибких шлангов. Гибкий шланг при распиле ГБЦ мне не понадобился. 2. Для распила желательно купить комплект любых шарошек, лишь бы подлезть. Понадобится при грубом убирании наплыва под направляющую в выпускном канале и для убирания резких перегибов в каналах, в общем.
После совмещения пилим каналы. Впуск распилился очень быстро и очень просто по сравнению с коллектором. Я очень обрадовался. Расточил. И думал, что так же легко расточу выпуск, ну чуть тяжелее из-за большего наплыва. Ошибался. Выпуск по сравнению со впуском пилится намного тяжелее, как раз из-за этого дурацкого, не понятного наплыва сделанного заводом…
В общем, я делал так
1. сначала шарошкой срубал направляйку по максимуму со стороны камеры сгорания
шарошим
2. Как только появилось место, чтобы подлезть шкуркой - точим…
срубаем её…
3. Срезали. Получаем канал, который уже в два раза больше стокового, хотя, срублен только наплыв.
наплыва нет
4. Затем, все подравниваем шарошкой и выводим наждачкой на гибком шланге и получаем такую красоту
каналы
Общий результат вы видели на первой фотографии.
33х29
ГБЦ получилась 33х29
2. Расточка ГБЦ ВАЗ 2105
Решил я поставить инжектор. Надоел мне этот "Озон", да и вообще попробовать немного раздушить мотор. Просто так ставить не интересно и решил расточить головку и коллектора. У меня было: -какие то две супер шарошки которые грызли и чугун и алюминий одинаково хорошо
-шарошка для раззенковки выпускного седла ваз 2101,30 градусная которая (острая, поднимает прихлоп) с наружным диаметром по краям фрез 35мм.
-дрель и сверло по бетону так как удобно наматывать тряпку (не рвёт и не проворачивает) -мерные клапана, обточенные до нужного размера
К сожалению нету фоток инжекторного коллектора в не расточенном состоянии. Изначально было: -каналы в ресивере 36мм -коллектор был с конусом (типа воздух там должен ускоряться) и с 36мм выходил на 28мм (около головки). -в ГБЦ вообще не понятные каналы ну в среднем около 28мм. А там, где стоит направляющая клапана вообще мало получается. Начал точить с коллектора, я думаю не стоит рассказывать, как наматывать тряпку на сверло, а на тряпку шкурку. Брал я кстати, самую злую и на тряпичной основе.
Проблема появилась в 1 и 4 трубе, там образовались дыры которые потом заварились.
Проверить насколько герметично заварено поможет 646 растворитель (удобней чем керосин так как быстро высыхает) и мел (лучше цветной). Далее натираем мелом место где приварена заплатка, а внутрь коллектора наливаем не много растворителя, бултыхем и там, где дырки мел начинает намокать и темнеть. Такой способ позволяет найти даже очень маленькие дырки. Растачивая коллектор, растачиваются и места посадки форсунок.
На этой фотке это не так страшно, но некоторые расточились так что форсунка уже не вставала герметично. Я взял сварочный электрод 2мм согнул кольцом и подложил под упор форсунки.
Проверил на герметичность мелом и растворителем, всё держит. Теперь нужно состыковать ресивер и коллектор. Там всё не так плохо, можно было и ничего не делать, но родная прокладка была больше чем каналы
Вырезал новую
А так как прокладка новая получилась тоньше, то и вторую нужно делать тоньше.
Коллектор готов.
Теперь его нужно без ступенек состыковать с ГБЦ. Берем ГБЦ, одеваем прокладку и оба коллектора. Чтобы все максимально точно сошлось при сборке я сместил прокладку максимально вниз (к блоку) на сколько позволили дырки под шпильки в прокладке. Слегка поджал гайками коллектора и обвёл очертания обоих коллекторов. Теперь всё разбираем, прикладываем прокладку к впускному коллектору, выравниваем по очертаниям которые в сборе с ГБЦ делали и поджимаем гаечками. Точил прокладку по форме каналов 1фрезой. Теперь прикладываем прокладку к ГБЦ так же как и когда мерили с коллекторами, т. е. смещая вниз на сколько возможно. Притягиваем гаечками и обводим все 8 каналов. Так как головка карбюраторная то появляется небольшая проблема
Одна головка не выдержала, или я ошибся много взял, или головка попалась тонкая
За то теперь можно было на ней все попробовать и посмотреть толщину стенок
Заход в головку я делал 1 фрезой во всех каналах.
Теперь берем фрезу 3 и проходим 4 впускных седла и немного алюминия в канале снял.
После этого можно выбивать направляющие (все 8) клапана и точить шкуркой.
Выпускные сёдла я расточил шкуркой и тряпкой до 29 используя мерный клапан
Общий вид
Направляющие клапана были подрезаны, забиты и шарошкой сточены в вровень с каналом
Теперь нужно стыковать Выпуск. Я грыз шарошкой №1.
В сборе выглядит
Теперь доработка тарелок клапана.
Цели преследовалось две: уменьшение веса тарелки, чтобы на оборотах клапан не завис и уменьшение натяжения пружины под распределительный валвал с другим подъёмом (пока остаётся родной вал).
Также по максимум были обточены рокера на наждаке для уменьшения веса. Итого. Машина завелась с первого раза всё чётко. Разгон до сотни 15сек. Настройка мозгов инжектора продолжаются.
3. ГБЦ прирезка седел и притирка клапанов ВАЗ 2101
Начал собирать ГБЦ и в процессе сборки решил все подробно описать. Направляющие втулки клапанов изначально лежали в морозилке. А головку я разогрел в духовой печи пока мамы не было дома) Это делается для того чтобы втулки было легче запрессовать. И все втулки я запрессовал специальным инструментом для запрессовки направляющих. К сожалению, фоток процесса запрессовки, я не сделал, так как не думал, что захочу все подробно описать
После того, как голова остыла, прошелся разверткой все втулки клапанов.
Вставив клапан, мы видим, что есть просвет, и надо его убрать
Для этого берем зенковки для прирезки седел клапанов
Для примера я покажу, как делается на выпускном седле. Вот так оно выглядело изначально
В начале берем фрезу 45гр.
Начинаем прирезать
После нескольких оборотов мы видим, что касание фрезы - только с одной стороны. Это означает что седло немного смещено по отношению направляющей втулки
Прирезаем до тех пор, пока касание не будет по всему периметру седла
После чего нам надо сузить рабочую фаску. Для этого берем фрезу 60гр.
И прирезаем
Потом прирезаем фрезой 30гр.
Вот что в конце получилось. Фаска 45гр. должна быть меньше 1мм. Я ее отметил красным пунктиром
Вот таким аналогичный образом прирезаются все остальные седла клапанов. После прирезки седел надо притереть клапана. Для этого берем специальную пасту для притирки клапанов и намазываем на фаску тонким слоем
Вставляем клапан и одеваем специальный инструмент для притирки
И притираем до тех пор, пока не исчезнет скрежет и звук не станет тихим. После чего, тряпкой убираем пасту с клапана и седла. Вставляем клапан и светим лампой со стороны камеры сгорания, а сами смотрим в канал и, как видим, просвета нет.
Так же аналогично притираем остальные клапана.
4. Капремонт ГБЦ ВАЗ 2106
Итак, началось всё с того, что у меня стала часто загораться контрольная лампа недостаточного давления масла. Поглядел на щуп — он сухой… ну так, на кончике была капелька масла! Да и с прокладки ГБЦ уже до этого начало выдавливать масло, что и послужило вскрытию головы. И когда очередь дошла до откручивания болтов ГБЦ, настала злостная и упорная борьба по их выворачиванию.
Итог 1-го дня — это ровно, как раз этот день, ушел на снятие головки. Болты прикипели так, что отвернуть их было очень проблематично. Сначала свернули вязы длинному воротку, квадратный конец, просто превратился в восьмёрку и так несколько раз… Отрезали болгаркой, обтачивали ею новые края, но метал был мягкий поддавался стойким болтам. Тут конечно еще сыграло то, что они у меня оказались нового образца М12…
12 versus 19
В итоге мы сумели сломать ключ под головку, 2 головки, они попросту лопнули и осталось 3 неподступных болта, слизанных "вхлам"!
слева кованная
Тут друг вспомнил, что знакомый на авторынке покупал спецключ, чтобы можно было справится с аналогичной проблемой. Оказалось, что существует набор спецголовок, но этот набор оказался стоимостью в 2400р. В итоге купили за 150р. кованную головку на 12 с надсечками внутренних граней. Приехали и тут же с помощью неё открутили 2 из 3-х слизанных болтов. Остался один, у которого стенки превратились под головку на 11. Поехали 2-й раз на рынок за аналогичной гаечной головкой на 11, но таких не оказалось в наличии. Пришлось купить на 10. Стали пытаться приблизить болт к 10-м размерам. Тут пошли в бой и зубило с молотком и напильник, но в итоге лопнувшая третья кованная головка и в бой пошла болгарка!
Распил ГБЦ
Срезали в итоге этот болт и сняли её, ура!
блок
И когда она была снята, то оказалось, что многое должно пойти под замену, и было куплено:
— Распределительный вал 21213 с постелью — Комплект клапанов ВАЗ — Автонатяжитель цепи Pilot — Рокера и солдатики — Маслосъёмные колпачки Goetz — Успокоитель цепи — Комплект болтов ГБЦ на 19 А также ремкомплект прокладок движка и масло на залив
Распределительный валвал 21213
Комплект клапанов ВАЗ
Автонатяжитель цепи Pilot
Маслосъёмные
Всё из-за неё началось
На 3-й день снова занялись ремонтом. Снятую голову очистили от грязи и отложений масла. Пролили керосином камеры сгорания. В итоге оказалось, что 2, 3 и 7-й клапаны пропускают. На самих же клапанах и седлах был шлак, как и в самих каналах, всё в чёрных ужасных отложениях.
проливаем клапана керосином
Прочистили каналы, рассухарили старые и поставили новые ВАЗовские клапана. Маслосъёмные колпачки оказались в дубовом и потресканом состоянии, на замену им, пошли зелёные "гётцы".
запрессовка колпачков
Притёрли рабочие поверхности и снова пролили камеры. Получилось с первого раза, керосин остался на месте.
седла притерты
Новые рокера и солдатики установили. Они так и не успели поработать на его машине, т.к. он поставил "гидрики".
рокера
Распределительный валтоже его, 213-й, он немного побегал, но совсем новый, т.к. у него теперь 214-й. Постель подобрали под вал у его хоршего знакомого-тёзки, который уже много лет торгует хорошими запчастями. Мои старый распределительный вал уже был с задирами, как и сама постель и сильно гремел при простукивании. Также купили новый автонатяжитель цепи "Pilot", ну и ремкомплект всех прокладок движка, масло "Petro Canada" разливное, ушло аж 1,5л.
Ну и несколько дней проковырялись со сборкой, а потом настройка клапанов по "рейке".
настройка
И только собрали всё под вечер, выгнали машину на улицу и тут хлынула фонтаном, тосольная трубка, идущая с помпы на печку. Открутили с другого двигателя нужную нам деталь. Установили её, поехали на заправку… Я собирался уехать домой этим вечером, но не тут-то было, 2-я подляна случиилась сразу, как только доехали до второго перекрестка и опять в виде утечки тосола. Теперь оказалось, что патрубок идущий с радиатора к помпе, потек у насоса. Виной всему сильно затянутый хомут. Пришлось остаться у друга в гостях еще на одну ночь. На утро сбегал в магазин и купил 2л тосола, а патрубок просто срезал до того места, где он разорвался. Получилось, длины хватило чтобы надеть. Тосол никуда уже не убегал. Вытеснили из системы воздух, настроили зажигание
5. Замена прокладки ГБЦ ВАЗ 2107
Все же умудрился я перегреть движок (сам виноват дурак, пожалел 100 руб. на датчик включения вентилятора, провел кнопку — вот и результат), патрубки радиатора надувались, словно воздушные шары. Закупился прокладками: прокладка ГБЦ под поршни диаметром 76мм (У меня блок 2103), прокладки впуск/выпуск коллекторов, прокладками карбюратора (его снимать необязательно, но я снял), герметик высокотемпературный, герметик резьбовой(у меня выкрутилось много гаек вместе со шпильками), прокладка клапанной крышки, прокладка крышки цепи(тоже снимать не нужно, просто я цепь менял заодно), прокладка приемной трубы глушителя(у меня на 4 болта), прокладки штуцеров шлангов печки и шлагов радиатора и немного тосола что бы потом долить.
Сам процесс. 1. Слил охлаждающую жидкость 2. Снял карбюр и все патрубки, идущие на ГБЦ, отсоединил приемную трубу глушителя. 3. Снял коллекторы 4. Отсоединил звезду распредвала. 5. Снял ГБЦ.
После чего отвез ГБЦ на шлифовку, карбюр на переборку мастеру.
На следующий день забрал голову
Отшливованная ГБЦ
Сняли 0.2 мм
Помимо прокладки ГБЦ заменил цепь, башмак натяжения цепи, натяжитель цепи, прокладки бензонасоса и карбюра, сальник коленвала.
Монтаж. Зачищаю блок под прокладку.
Инструмент для зачистки. Хим. средства не использовал для удаления старой прокладки, а ежик на дрель мне показали уже после установки ГБЦ))
Зачистка.
Готово
Рассказывать в принципе нечего, по мурзилке можно сделать все самому, был бы инструмент, но есть некоторые нюансы. Перед установкой, помимо очистки поверхности, надо из отверстий под болты крепления ГБЦ откачать масло (если есть) во избежание гидроудара при затягивании болтов. Я использовал шприц с натянутым на него шланчиком. На герметик посадил штуцер патрубка печки и штуцер шлагов радиатора (разумеется с прокладками). Прокладки коллекторов и ГБЦ сажать на герметик НЕ НАДО. При желании можно поменять масло, отрегулировать клапана и поменять опоры движка попутно (пока все снято), что я и осуществил.
6. Замена направляющих ВАЗ 2101
Затянулся у меня ремонт по замене масл. колпачков, придется менять сами направляющие, сегодня снял ГБЦ, распряг клапана, колпачки конечно не в лучшем виде — что и требовалось ожидать. Начинается все с открытия капота.
Ну и начинаем по немного разбирать, снимаем распред.вал
снимаем рокера, и складываем на дощечку
Сохранить в Альбом
После того, как распряг клапана, - посмотрел на колпачки. Сначала думал, что их там вообще нет, но они там были, но не в лучшем виде.
Но вот и снял ГБЦ, поршня конечно в "хорошем" нагаре, ну, ничего - счистим
Теперь буду менять направляющие.
Сегодня купил направляющие и колпачки, вынул клапана, отмыл ГБЦ.
Меняли сами втулки таким образом: на холодную спец. оправкой их выбивали, а забивать нужно на горячую, т.е. чтобы ГБЦ была нагрета, но, как мне подсказали, не выше 80 градусов, а втулки должны быть холодными, если клапана не будут лезть, то придется втулки развернуть разверткой на 8, но она мне не понадобилась. Грел я паяльной лампой.
При замене клапанов потребуется править седла зенковками и притирать клапана спец.пастой, но я не менял клапана, поэтому только притирал.
Притирал следующим образом: на дрель с подходящим сверлом надел бензиновый шланг, а другой конец надел на клапан, оба конца закрепил хомутами, и притирал в одну потом в другую сторону, на каждый клапан минут 5-10, но это потому что они у меня уже стояли, с новыми придется повозиться подольше.
Но потом мы придумали круче. Так как у меня есть прорези в клапанах, мы взяли от шуруповерта насадку и крутили уже с другой стороны.
После, - надели колпачки. На этот раз зашли " как по маслу" и в прямом и в переносном смысле. Как только один притерли, цилиндр сразу запрягаем.
Основной этап закончен, - осталось поставить на блок.
https://www.drive2.ru/l/288230376152062383/, https://www.drive2.ru/l/4899916394579235162/, https://www.drive2.ru/l/288230376152803553/, https://www.drive2.ru/l/288230376152213996/, https://www.drive2.ru/l/288230376153111424/, https://www.drive2.ru/l/4131589/,
https://www.drive2.ru/l/292436/, https://www.drive2.ru/l/297318/, https://www.drive2.ru/l/317593/
следующая статья:
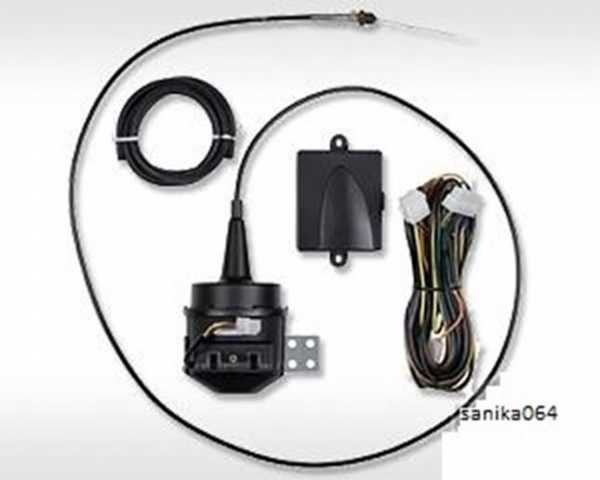
Установка круиз-контроля на ВАЗ 2106
Т.к машина используется исключительно для дальних поездок, то не удержался и поставил круиз контроль Waeco MagicSpeed…
remont-vaza.ru
Доработка ГБЦ на автомобилях ВАЗ 2101 - 2107 своими руками - Тюнинг двигателя - Тюнинг "Классики" - Тюнинг
Для начала расчеты. Тупо площади считаем.
Карбюратор вебер дырки 24х24,
(24*24*3,1415/2)*2 = 904 мм2
Впускной канал, самая узкая часть - там, где выпирает направляющая.
(29*29*3,1415/4)-(14*14*3,1415/4) = 660 - 154 = 506 мм2
Щель впускного клапана в максимальном подъеме:
33*3,1415*10 = 1037 мм2
Отсюда видно, что размеры канала значительно уступают по сравнению с другими узкими местами впускного тракта. Это действительно только в момент полного открытия клапана, но это время почти полного открытия подавляющее. Короче, нада делать.
Максимум (покажу на фото) - это 34мм, на большее стандартный коллектор не расточить, стенка 1мм остается.
Считаем с учетом того, что клапанную ножку обточим до 7мм, а направляющую срежем заподлицо:
(34*34*3,1415/4)-(7*7*3,1415/4) = 909 - 39 = 870 мм2
получается, увеличиваем площадь самого узкого места на 70%, неплохо...
Начнем с замера мощности:
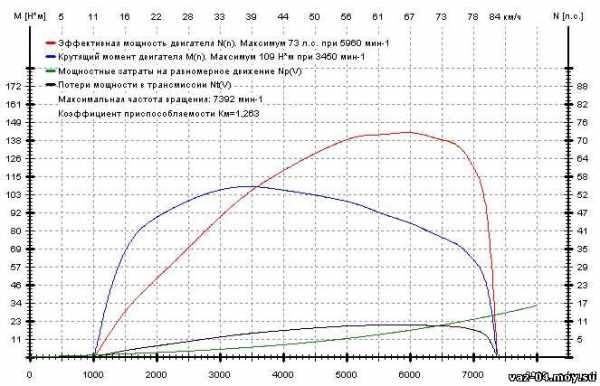
Абсолютные данные не точные, но в сравнении - ценная информация.
От составителя: Двигатель 1300, ГБЦ 2101, система питания Webber 2101 23х24
Далее голова снимается с машины, разбирается и моется.
Шикарно конечно моется углекислотой, но не было огнетушителя под рукой. Мыл обычным керосином, а потом в ванной щеткой с порошком. Кстати, нужно не забыть смазать маслом все стальные детали (направляющие, седла, втулки под рокера), чтоб ржа не схватила.
Еще неплохой по слухам метод, когда ВД40 растворяется в незамерзайке. жидкости для омывателя - получается белая эмульсия, которая все смывает легко...
Шпильки, кстати, лучше тоже скрутить, но мне покуда не мешали...
Пациент:
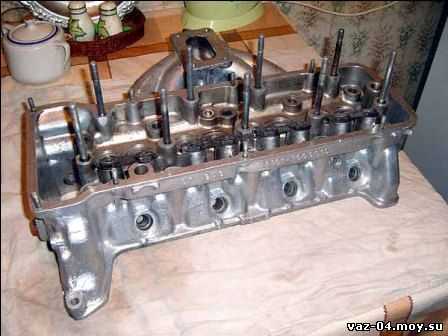
Направляющие выбиваются приспособлением, которое я изготовил из болта. Выбиваются легко и непринужденно... наружа приспособы 13.5, внутренний штырь для направления - 8мм.
Теперь все готово для пиления каналов. Я бы советовал начинать с коллектора, поскольку в голове запаса металла по краям больше, лучше подгонять голову под коллектор а не наоборот...
Замеры: каналы в голове 29, выпуск 27, в коллекторе - 29, вып. коллектор 29.
растачивал я шкуркой в дрели. Самая эффективная головка ИМХО - это вал (в моем случае сверло толстое), на который наматывается ветошь, а на нее - полоса шкурки дето в 20см длиной (ессно все внахлест мотается, чтоб не соскакивало)
Использовал я самую грубую шкурку НА ТРЯПИЧНОЙ ОСНОВЕ какая только была под рукой - это 24-ка. Один канал в голове я ею делал за 2 часа.
Также для удобства сделал наборчик шайб на палочке (см. фото), номинальной (34мм) и уменьшенного диаметра (33) и комплект для выпуска. Такими ну очень удобно контролировать диаметр канала, чтоб не махнуть лишку - такая шайба должна свободно проходить по каналу перпендикулярно оси, и не сильно болтаться.
Технология - мотаем ветошь со шкуркой так, чтобы "головка" еле лезла в дырку, начинаем сверлить потихоньку пропихивая все дальше, покуда шкурка не рассыплется. Потом можно кусок оторвать или перевернуть полоску и заново... Контролируем диаметр шайбой, новую полосу шкурки и заново поехали...
неплохо бы еще заиметь инструмент для измерения толщины стенок, но я пользовался пинцетом с налепленными на концы кусочками пластилина.
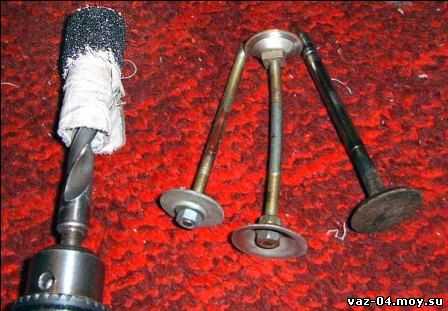
Коллектор:
разительно отличаются по диаметру пропиленные каналы от не пропиленных:
коллектор точится значительно тяжелее чем голова, из-за того, что можно подлезть только с одной стороны (со стороны карба не сильно то и просунешься).
Смог пропилить коллектор до 34-х только на 2/3, пришлось устранить сверлом перегородку между каналами:
как было
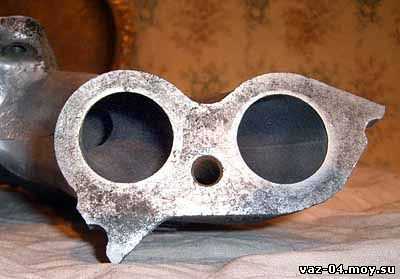
как стало
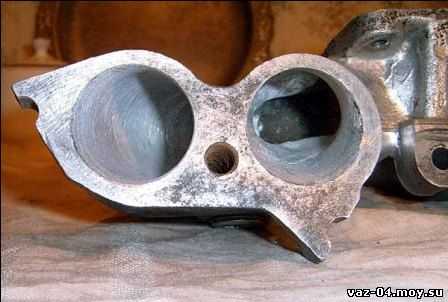
Все, шайбы свободно проходят:
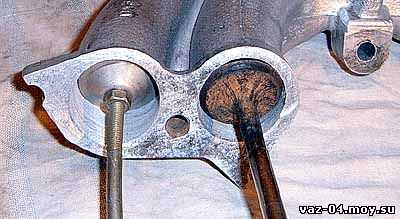
Теперь очередь головы.
Нужно состыковать каналы коллектора с головой. Пробовал разные варианты с отпечатками и проч... сложно все это как-то... Остановился на пластилине - леплю по окружности на голове, смачиваю водой коллектор, прижимаю рукой, отпускаю, выдавленный пластилин внутрь коллектора срезаю - четко видно, куда нужно править голову.
Поправить лучше отдельно перед расточкой, потому что шкурка раздает во все стороны одинаково. Поправить можно напильником круглым, я просто грубо обтесал дырку в нужную сторону, чтобы она равномерно повторяла контур дыры в коллекторе. Кстати, лучше выход из головы сделать чуть побольше, например 35, потому что ступенька все равно будет, лучше чтобы она была не в сторону головы. Но специально расширять не нада - 35 и так получится от постоянного шныряние шкуркой через эту дырку.
А потом поехали... Растачиваем равномерно со стороны коллектора, покуда шайба не будет пролазить до дырки под направляющую, потом лучше точить со стороны КС. С этой стороны осторожнее с седлами!!! Растачиваются они на удивления быстро и легко, можно полностью уничтожить место под фаску.
разница очевидна:
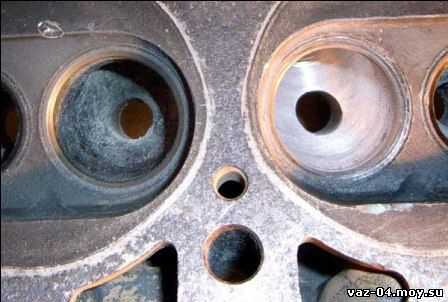
Хорошо видно, как убирается нарост вокруг дырки под направляющую, который очень неслабо закрывает канал:
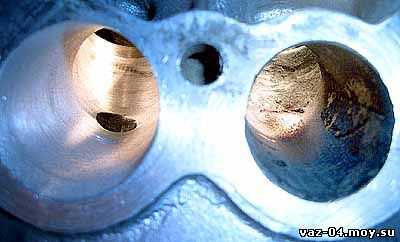
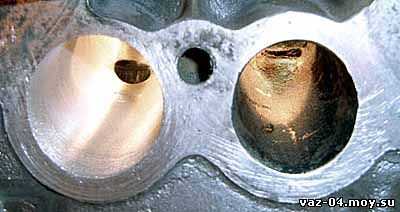
Каналы все пропилены, голова вымыта. Не забыть все стальные части перед мойкой смазать маслом, седла клапанов в первую очередь!). Для промывки системы охлаждения использовал электролит для акку - т.е. серную кислоту. Перевернул голову вверх тормашками, закупорил все отверстия и аккуратно, чтоб кислота не попала на наружную поверхность головы (она все ж алюминий хорошо ест), заливал внутрь, медленно покачивая голову. Накипь, налет и ржа растворяется полностью за несколько секунд, полный цикл возни головы в кислоте не думаю, что нужно растягивать более чем на 5 минут. Также аккуратно кислоту сливаем.
На фото отлично виден уровень стояние кислоты - сверху все грязно, снизу девственно чистый алюминий:
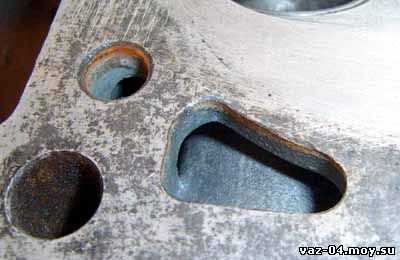
После голову сразу промыть, можно в растворе соды или стирального порошка и побыстрее высушить. Например, в духовке =)
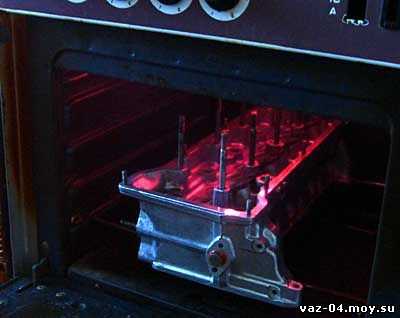
Итого:
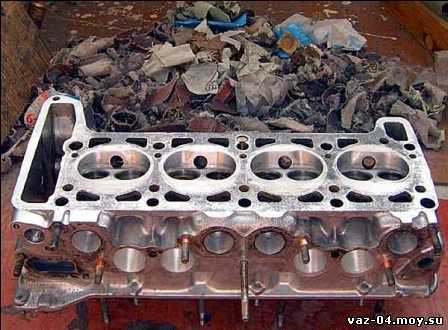
впуск коллектор 34 (было 29), каналы 34 (было 29), седла 33.5 (было 32.5)
выпуск каналы у седла 28 (было 27, наполовину перекрыты выступом под направляющую), на выходе из головы 30 (было 27), коллектор 30(таким и был), седла 28 (были 27.5).
Ушло 0.5 м2 шкурки №24 и гдето столько же ветоши. На канал в впускном коллекторе уходило 2 часа, в голове впуск - 1 час. В голове выпуск - пол часика...
Нарезал небольшие ушки в КС:
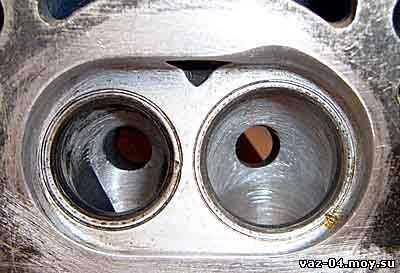
Результаты - в голове глядя на вход в канале, можно увидеть выход, в недоработанной такого нет:
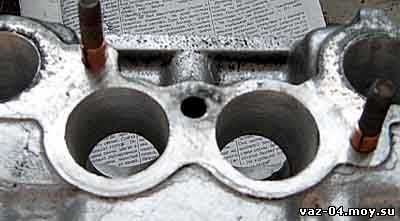
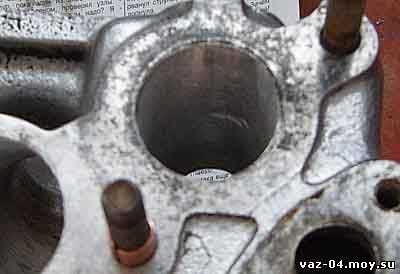
Теперь насчет направляющих. Тщательно взвесив все за и против, решил остановиться на своем варианте и пилить ее сложно-пространственно
Для начала разметил на ней метчиком линию, по которой она торчит в канале, также по всему периметру (чтоб легко точить и потом запрессовывать) прочертил ее перед и зад.
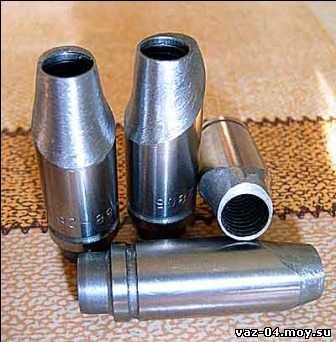
Смысл был в том, чтобы максимально снять торчащего металла, и в то же время оставить по максимуму по площади канал изнутри (масло) и не трогать вообще ее нагруженную сторону (разобьет), и при этом все максимально аэродинамично сгладить.
Впускные получились по оконцовке такими:
Как видно, на пятке (та сторона, на которую давит при работе клапан) я практически не трогал металл, поэтому вряд-ли деформируется.
С выпускными немного тяжелее - там и отвод тепла и нагруженность сильнее, и направление потока больше. Поэтому смысл такой-же, но объем работ значительно меньше:
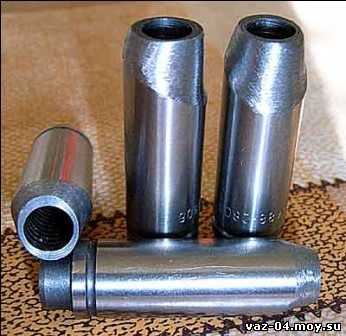
Вот так торчит стандартная в обработанном впускном канале:

вот так - обработанная (правда не до конца выведена, это бушная, я ее точил на пробу)
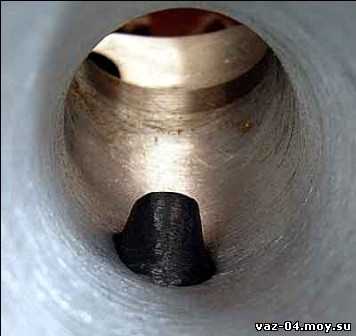
Доработал клапана...
Тяжеловато было, резец очень плохо берет, даже победитовый... Новый выпускной клапан практически вообще не берется, мне советовали на доработку брать только б/у, они лучше точатся - материал мягче.
Зато потом зажал в дрель и доводил форму шкуркой - берется на ура! Медленно зато уверенно снимается металл.
Вот что получилось в итоге:
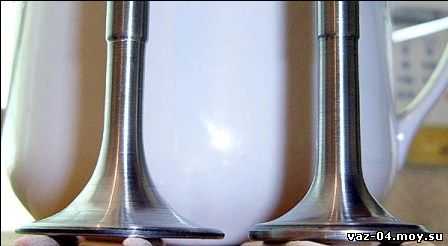
Снимался металл вот так:
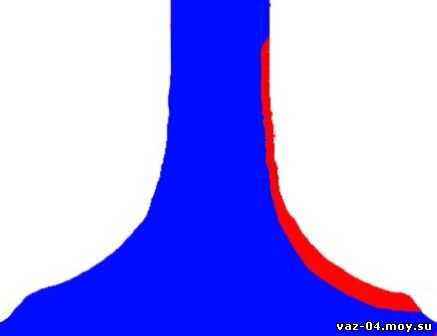
(обработанная фотка стокового впускного клапана, красным - снятый металл)
Запрессовал направляющие изготовленной оправкой (стальной прут, внутри отв. 11.0мм) Голова в духовке до 100 град, направляющие в морозилку. Забивать надо аккуратно, но очень быстро. Не забыть снять шпильки распреда, они будут мешаться (без снятия крайних вообще не запрессовать). Сначала лезет легко потом нагреваются, но все равно лезут нормально. Выбивались, чесслово, с гораздо большим усилием. Главное, шустрее орудовать.
Фото впуска с клапаном:
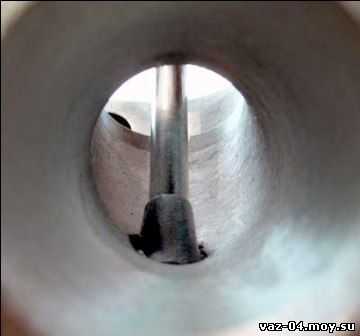
Выпуск с клапаном
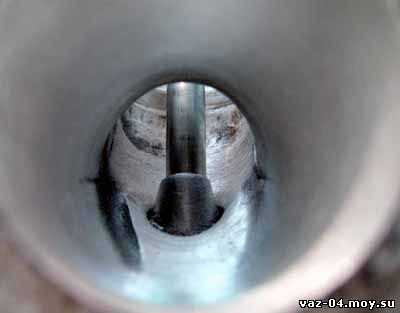
ГТЖ вместо 135/125 ввинтил 140/140. Немного покатался для небольшой приработки, померился.
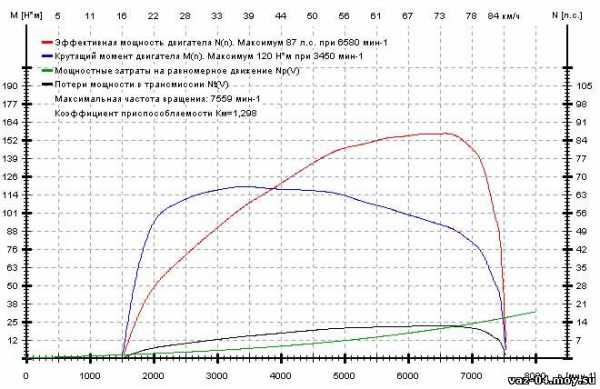
Как и следовало ожидать, ровный рост КМ по всей кривой, увеличение оборотов ММ, увеличение КП.
Прибавка получилась 14 лошадей (ну или 12, если учесть, что в молодости мотор имел 75), на что предварительно и рассчитывалось.
Ну, думаю, окончательной тарировкой карба еще одну-другую лошадку сниму (поскольку вроде и так едет нормально, без провалов)
Если все мои изыскания сжать в единый временной промежуток и выбросить эстетику (вроде надраивания до блеска головы), то в 5 рабочих дней уложиться можно легко. 1 день - снятие-установка-настройка, 3 дня пиления и 1 день на расслабоне посвятить можно клапанам.
vaz-04.moy.su